Applications :: Tail Gas Compressors
Case study 3: Tail Gas Compressor with H2S removal at Mazeikiai, Lithuania
|
|
Application: Off Gas Recovery
System: Tail Gas Compressor for vacuum unit
Location: Mazeikiu NAFTA refinery, Lithuania
INTRODUCTION
Reducing H2S and CO2 emissions is of great importance to the refining, gas-processing and petrochemical industries due to increasing environmental constraints. The unique Hijet compression system for vacuum unit off-gas was installed in December 1997 at Mazeikiu Nafta Refinery, Lithuania and has been in uninterrupted service since. The Hijet system is based on liquid jet technology, and employs a venturi device with amine solution (20% MEA) as the motive liquid. The off-gas contains a considerable amount of condensable vapors and high quantities of sour gases. The system simultaneously reduces the H2S content and boosts the gas pressure to 2.5 barg for use in the vacuum heater.
|
THE CHALLENGE
In this project the challenge was to solve the problem of safely burning the sour off-gas that contains air from in-leakages into the vacuum column thus constituting a fire risk. These gases were burned with low-pressure gas burners in the vacuum furnace, but they contributed to the refinery’s SO2 emissions. Inherent to the use of low-pressure burners is unstable flame operation and flame impingement. The inclusion of low deltaP flame arrestors that often blocked, required frequent operator intervention thus rendering the whole system ineffective. The throughput and/or heater outlet temperature had to be compromised. The solution of sending it to flare had on
occasion caused fire within the pipes thus demanding a whole new approach to solve these problems.
|
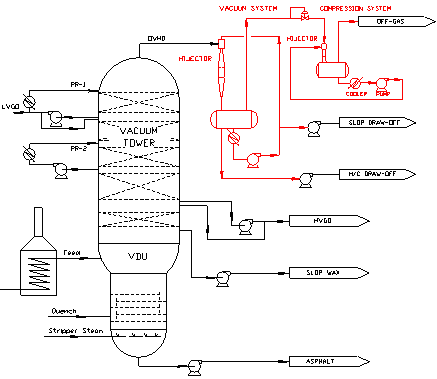 |
HIJET SOLUTION
The system is based on liquid jet technology and employs the Hijector™ - a liquid jet ejector of proprietary design. Amine solution (20% MEA) is used as the motive liquid.
The system simultaneously reduces the H2S content and boosts the gas pressure to 2.5 barg for use in the vacuum heater. The compressor suction is connected to the vacuum tower's overhead separator drum and the compressed gas is discharged into the vacuum heater gas burners without the need for further gas treatment.
The off-gas is contacted with the atomized MEA solution in the ejector and results in an outlet gas H2S concentration of
<600ppm. Further reductions in H2S concentration can be achieved by using other amine solutions and/or higher concentrations, increasing the separator discharge pressure, and installing additional contacting internals in the separator such as structured or random packing to increase the number of theoretical stages.
|
The design conditions and acceptance test run data are shown in the table.
Design Parameter | Process Specification | Acceptance Test-Run |
Suction Pressure | 0.40 Bara | 0.40 Bara |
Suction Temperature | 60 C | 45 C |
Flow Rate Gas | 2000 Nm3/h | 2000 Nm3/h |
H2S in Soar Gas | 30% | 12% |
H2S in Sweet Gas | <1000ppm | <1000ppm |
Discharge Pressure | 2.5 Barg | 2.5 Barg |
Discharge Temperature | 45 C | 42 C |
Motive Fluid | MEA 20% | MEA 20% |
Motive Fluid Flow Rate | 268 m3/h | 260 m3/h |
Motive Fluid Temperature | 50 C | 42 C |
Motive Fluid Pressure | 18 Barg | 16.8 Barg |
Motive Fluid Make-up | 10 m3/h | 10 m3/h |
|
CONCLUSIONS |
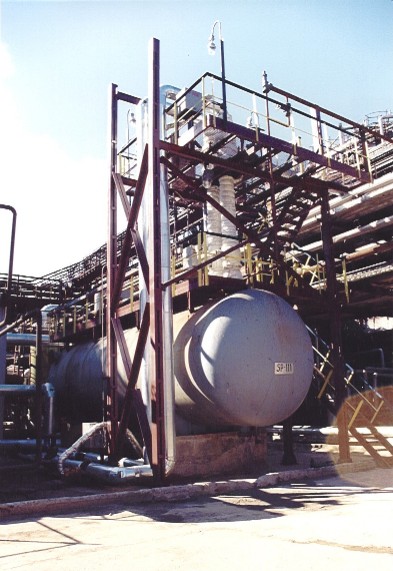 |
SYSTEM BENEFITS
- Utilization of the off-gases in the vacuum heater without sending them to the amine unit in lagged and heat traced piping.
- Eliminates problems related to the burning of low-pressure off-gases in the heater furnace.
- Frequent cleaning of plugged flame arrestors is unnecessary since these have been removed. The liquid seal in the separator would act as a flame arrestor.
- Reduced operational expense compared with a mechanical compressor while increasing reliability.
- The control of this system is simple by comparison to mechanical compressors.
|
© 1995-2025 Hijet Engineering Ltd |||||