Applications ::
Case study 6: Vacuum Distillation Unit at API Ancona Refinery, Italy |
|
Application: Vacuum Distillation
System: Visbreaker vacuum system
Location: API - Ancona refinery, Italy
INTRODUCTION
API decided to increase bitumen production capacity by installing a new Visbreaker Vacuum flash column. The limitations of inadequate soar water treatment and cooling water capacity were overcame by utilizing the unique Hijet vacuum system.
CHALLENGE
The use of conventional steam ejector system for the new column was considered prohibitively expensive because refinery had to overcome bottlenecks in the following utilities:
- Sour water treatment capacity
- Cooling water limitations
|
HIJET SOLUTION |
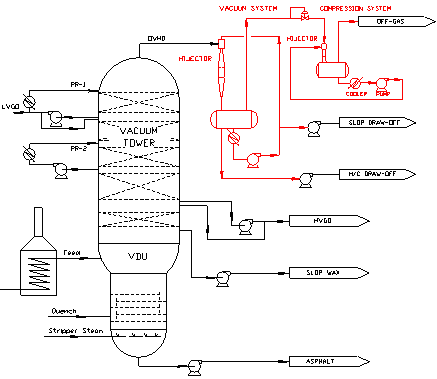 |
A two stage Hijet vacuum and compression was put into operation system at API Ancona refinery in February 2001 and has been in reliable service since. The first Hijector™ is mouinted to the side of the vacuum column without the necessity to build a separate structure. This reduces capital costs and required plot space. The first stage pulls vacuum at the top of the column to 15mm Hg whilstthe discharge pressure downstream the second stage is 2 bara. The system utilizes a single pump for both stages and LVGO as the motive liquid. The system also includes two separators, and one cooler.
|
CONCLUSIONS |
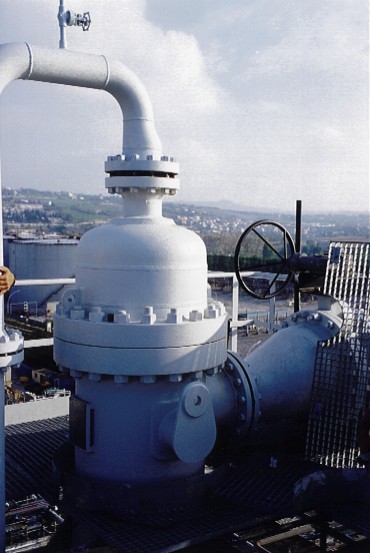 |
Hijet vacuum system at API refinery does not produce soar water and has only 25% of cooling water requirement compared to a steam ejector system, whilst at the same time provides the following additional benefits:
SYSTEM BENEFITS
- Increased reliability,
- No motive steam – reduced emissions,
- No sour water production– reduced emissions,
- Reduced operational expense compared with the steam ejector system.
|
The benefit of using the Hijet system is made clear by examining the data shown in the following table
Parameter | Steam Ejector System & LRP | Hijet two-stage vacuum-compression system |
Vacuum column pressure | 15 mm Hg | 15 mm Hg |
Discharge gas pressure | 1.5 bara | 1.5 bara |
Motive steam consumption | 9.0 tons/h | 0 tons/h |
Cooling water consumption | 639 m3/h | 128 m3/h |
Electric power Requirement | 15 kW (LRP) | 393 kW |
Operation time (350days / year) | 8,400 h | 8,400 h |
HP steam consumption / year | 75,600 tons | 0 T |
CW consumption / year | 5,367,600 m3 | 1,075,200 m3 |
Electric Power consumption /year | 126,000 kWh | 3,301,200 kWh |
Cost of HP steam / year | EUR 756,000 | 0 |
Cost of cooling water / year | EUR 161,028 | EUR 32,256 |
Cost of electric power / year | EUR 5,670 | EUR 148,554 |
Total cost of utilities / year | EUR 922,698 | EUR 180,810 |
Minimum yearly direct saving | 0 | EUR 741,888 |
|
© 1995-2025 Hijet Engineering Ltd |||||