Company :: Hijector™ Installations
Company Name | Location | System | Application |
CPC Linyuan | CPC Linyuan, Taiwan (Site-1), (Site-2) | Compression system (2 sites x 2 Trains) | Flare Gas Recovery |
CPC Taoyuan | CPC Taoyuan, Taiwan | Compression system (2 Trains) | Flare Gas Recovery |
CPC Talin | Talin, Taiwan | Compression system (2 Trains x 2 Units) | Flare Gas Recovery |
SINCLAIR OIL | Wyoming Sinclair refinery, WY, USA | Compression system | Flare Gas Recovery |
CNPC | Huludao (Jinxi), Liaoning, China | Compression system | Tail Gas Compression System |
EXXON MOBIL | Fos-Sur-Mer, France | Compression system | Tail Gas Compression System |
MURPHY OIL | Mereaux, LA, USA | Compression system | Flare Gas Recovery |
CNPC | Golmud, Qinghai, China | Vacuum system | Vacuum Distillation Unit |
CHEVRON PRODUCTS | Pascagoula, MS, USA | Compression system (3 trains) | Flare Gas Recovery |
CHEVRON PRODUCTS | El Segundo, CA, USA | Compression system (3 trains) | Flare Gas Recovery |
SHELL | Shell Raffinaderi AB, Gothenburg, Sweden | Compression system | Membrane Hydrogen Recovery |
EXXON MOBIL | Sicily, Italy | Compression system (2 units) | Tail Gas Compression System |
API OIL | Ancona, Italy | Vacuum system | Visbreaker Vacuum Flash Column |
ORLEN (MAZEIKIU) NAFTA | Mazeikiai, Lithuania | Vacuum system | Vacuum Distillation Unit |
ORLEN (MAZEIKIU) NAFTA | Mazeikiai, Lithuania | Compression system | Vacuum Distillation Unit - Off gas Recovery |
SINOPEC | Tahe, China | Vacuum system | Vacuum Distillation Unit |
AZERNEFTYANAJAG | Baku, Azerbaijan | Vacuum system | Vacuum Tower |
DOW CHEMICAL | Freeport, TX, USA | Vacuum system | Chemical Reactor |
SCHNECTADY | Freeport, TX, USA | Vacuum system | Alkylated Phenol Unit |
CHEVRON PHILLIPS | Borger, TX, USA | Vacuum system (2) | Merc/Poly Tower |
MURPHY OIL | Mereaux, LA, USA | Compression system | Vent Gas |
LEE COLLEGE | Baytown, TX, USA | Compression system | General purpose Air compressor |
SASOL | Westlake, LA, USA | Compression system | Hydrogen Recovery |
NESTE | Porvoo, Finland | Compression system | Sour Water Feed Tank Vent Gas Compressor |
CPC Linyuan, Taiwan |
Two sites, each has 2 trains, and each train consists of 2 Hijectors®, 1 pump, 1 heat exchanger, 1 separator. |
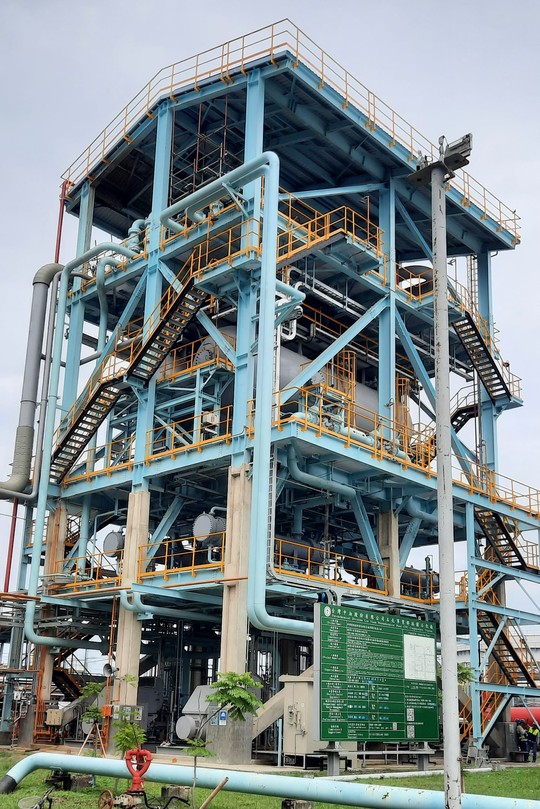 |
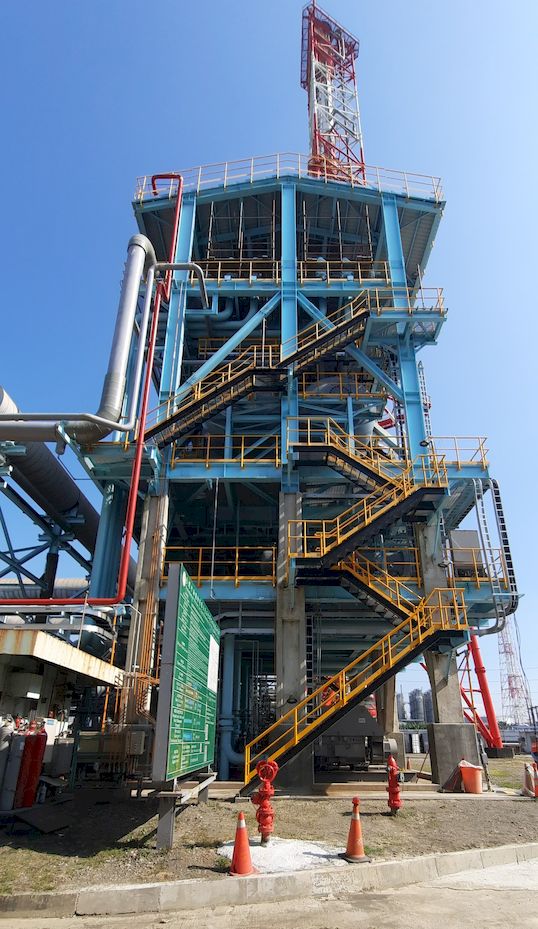 |
CPC Taoyuan, Taiwan |
First liquid ejector FGR system in the world with automatic Hijector® and pump staging up and down based on flare header pressure with a nominal capacity of 5.8 MMSCFD.
- Hijet delivered actual capacity of over 15% above the design requirement.
- One area with a total of 2 trains, each train consisting of 2 Hijectors®, 2 pumps, 2 heat exchangers, 1 separator.
- No shutdown of the system since commissioning in 2015
- Maintenance is limited to cleaning the motive liquid filters due to a significant particle content from the flare header.
- Refinery has been able to achieve practically zero flaring.
- Refinery has not used any anti-foaming chemicals in the amine absorber column because the sour water motive liquid Hijector® system washes the gas of any particles and absorbs CO2 and NH3 before sending the gas for amine treatment.
|
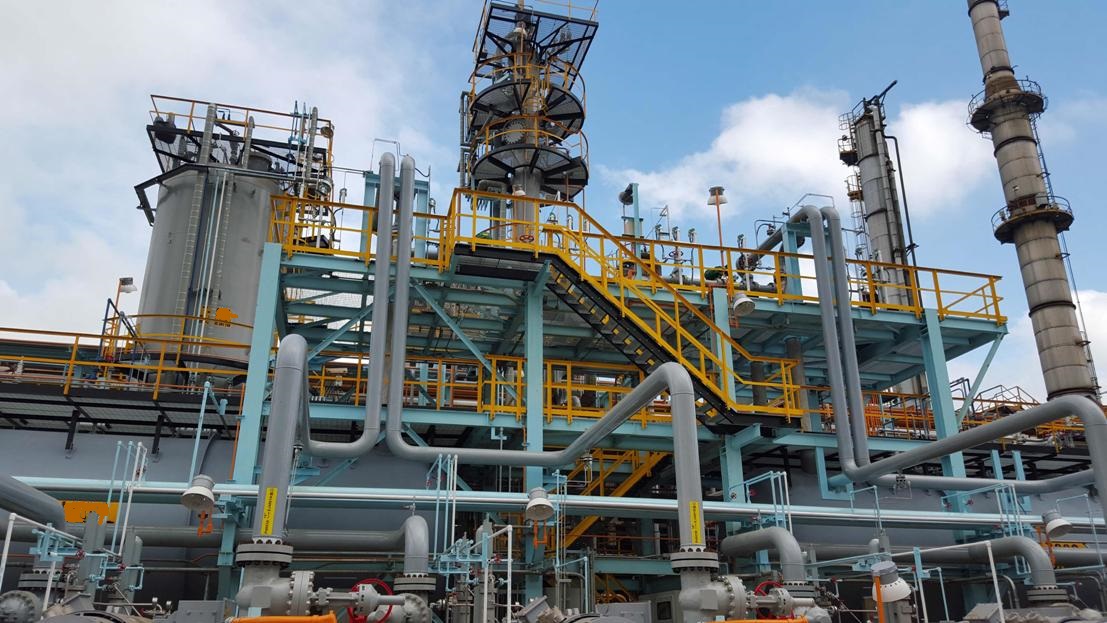 |
CPC Talin, Taiwan |
Largest liquid ejector FGR system in the world with a nominal capacity of 18
MMSCFD.
- Hijet delivered actual capacity of over 30% above the design requirement.
- 2 separate areas with a total of 4 trains, each train consisting of 2 Hijectors®, 2 pumps, 2 heat exchangers, 1 separator.
- No shutdown of the system since commissioning 2 years ago.
- Maintenance is limited to cleaning the motive liquid filters every 8 hours due to significant particle content from the flare header .
- Refinery has been able to achieve practically zero flaring.
- Refinery has not used any anti-foaming chemicals in the amine absorber column because the sour water motive liquid Hijector® system washes the gas of any particles and absorbs CO2 and NH3 before sending the gas for amine treatment.
|
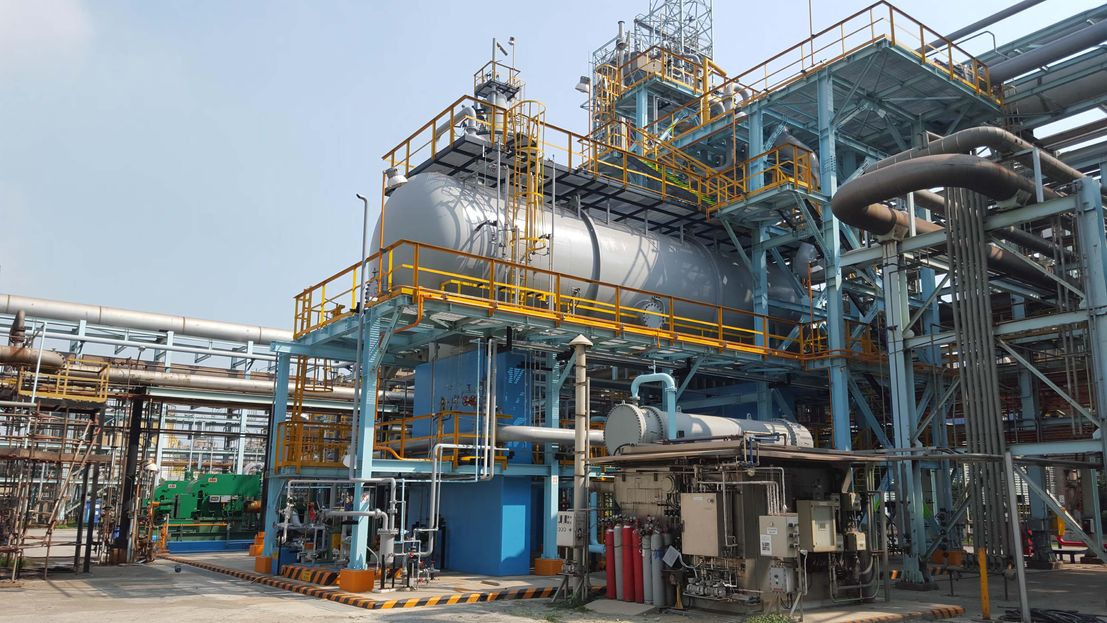 |
Wyoming Sinclair refinery, WY, USA |
At Sinclair refinery, the biggest ever single Hijector unit is used for flare gas recovery. |
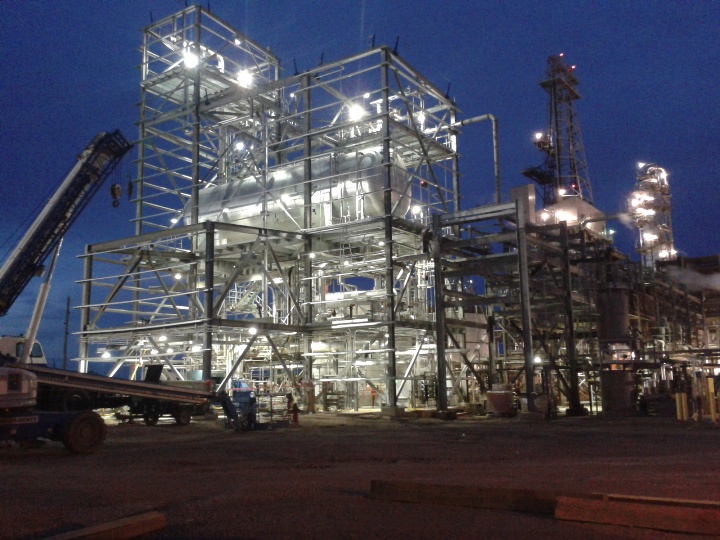 |
Chevron El Segundo, CA, USA |
At El Segundo refinery, the latest liquid jet technology is used for flare gas recovery. The Hiject compression system provides the ideal solution to deal with the new environmental challenges facing the modern refining industry ... (Case study) |
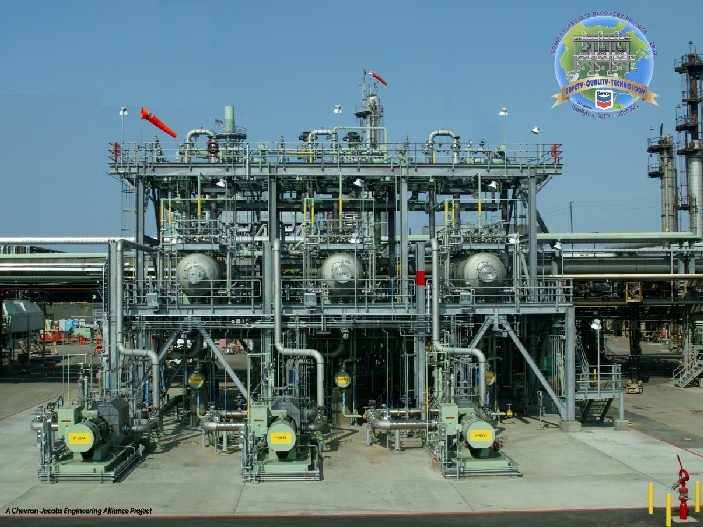 |
API Ancona Refinery, Italy |
API - Raffineria di Ancona has been using LG-Jet vacuum and off-gas compression equipment at Falconara M. refining facility in Italy.Currently it is used to produce vacuum in the Visbreaker vacuum flash column while discharging the off-gas above atmospheric pressure ... (Case study) |
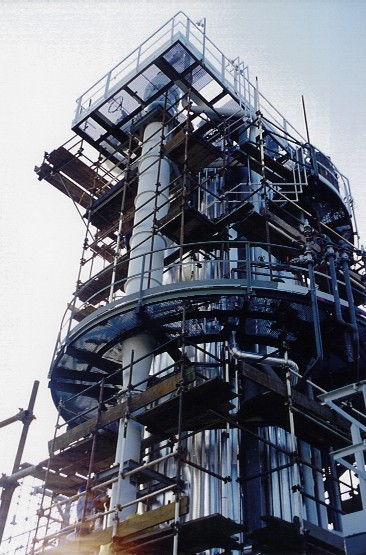 |
Shell Raffinaderi AB, Gothenburg, Sweden |
In this project the challenge was to recover the high value hydrogen from the hydrotreater LP separator off-gas which contains a considerable amount of hydrogen, hydrocarbons and high quantities of H2S ... (Case study) |
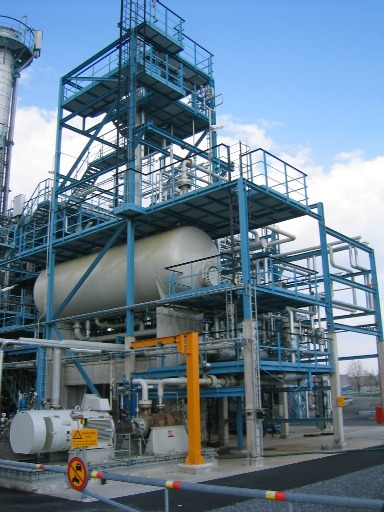 |
ORLEN (former Mazeikiu) Nafta, Lithuania |
ORLEN (Mazeikiu) Refinery has been using LG-Jet vacuum and off-gas compression
equipment since 1995.Currently it is used to produce vacuum in the vacuum distillation column for the crude residue from the atmospheric distillation system. Throff-gas of the vacuum tower is discharged above atmospheric pressure ... (Case study) |
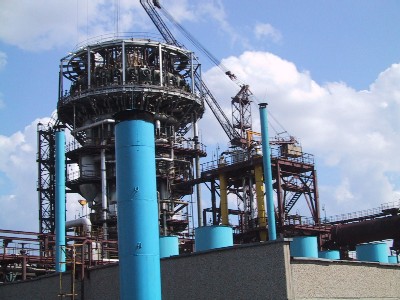 |
EXXON MOBIL Augusta Refinery |
Two Hijet Compression Systems based on the Liquid Jet Technology have been installed at the Esso Augusta refinery in Sicily to boost the off gas pressure to acceptable levels to be able to send them to an amine treatment unit ... (Case Study) |
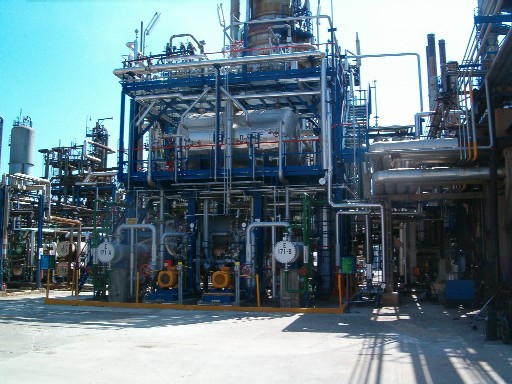 |
SINOPEC Tahe Refinery |
Tahe refinery faced continuous problems with their existing steam ejector system that required
regular maintenance due to corrosion problems ... (Case study) |
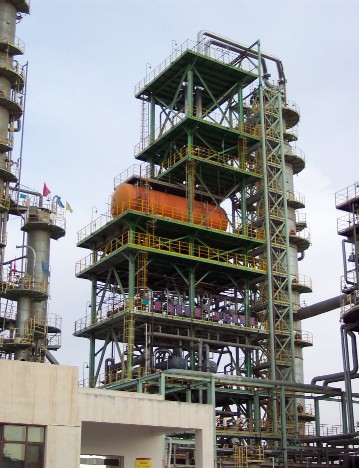 |
Geermu CNPC Refinery |
A new vacuum column required a new technology to achieve vacuum of about ~1kPa. |
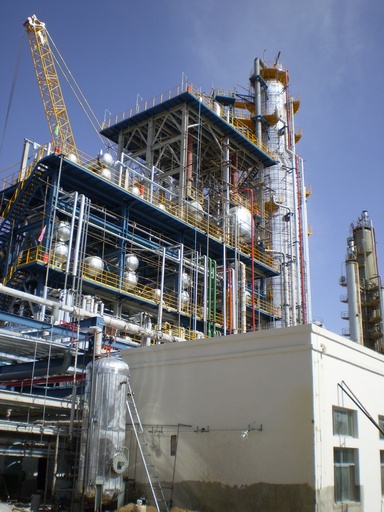 |
© 1995-2025 Hijet Engineering Ltd |||||